Activity Based Costing : méthode d'analyse des coûts par activité
Sommaire
C’est un principe bien connu : une minorité de nos services génèrent la majorité de notre chiffre d’affaires. C’est aussi vrai dans le domaine de la logistique. Une minorité des produits que vend une entreprise aux consommateurs lui rapporte plus que tous les autres réunis. Pour les identifier, une méthode a fait ses preuves : la méthode ABC. Sur la base des coûts réels engendrés par un référentiel, le réapprovisionnement de celui-ci sera plus ou moins prioritaire. Et cette méthode consiste justement à classifier les articles en fonction de leur rentabilité.
Méthode ABC : qu’est-ce que c’est ?
La méthode ABC (Activity Based Costing) s’appuie sur le principe de Pareto : 20 % des produits génèrent 80 % du chiffre d’affaires (CA) d’une entreprise. Cette loi s’applique également dans le milieu de la logistique et la méthode ABC aide à identifier quels référentiels sont les plus rentables en se basant sur le coût à base d’activité.
Les produits sont classés en 3 catégories (A, B et C), chacune définissant l’importance du produit pour le CA.
- « A » comprend les articles les plus rentables ;
- « C » ceux n’apportant que peu de rentrées d’argent ;
- « B » est la catégorie intermédiaire.
Ce découpage stratégique des activités de l’entreprise permet d’établir un ordre de priorité quant aux référentiels pour lesquels il faudra se réapprovisionner bien avant la rupture de stock. Ceux appartenant à la catégorie A, étant les plus rentables, seront donc commandés auprès du fournisseur beaucoup plus tôt que ceux appartenant à la catégorie C.
Ainsi, la gestion des stocks dans l’entrepôt sera adaptée pour coller aux besoins logistiques afin d’optimiser le traitement des commandes. À noter que cette classification n’est pas éternelle : la demande étant en constante évolution, l’ordre des priorités l’est aussi.
Mais à partir de quand un référentiel est-il rentable ? On le considère rentable si son coût de production se trouve sous le seuil de rentabilité. Et entre dans le calcul des coûts de production les inducteurs de coûts générés par l’activité que nécessite la production du produit.
Les étapes de la méthode ABC
Respecter ces 5 étapes, c’est s’assurer une meilleure gestion de ses ressources :
- Identification des activités clés de l’entreprise ;
- Choix des inducteurs de coûts ;
- Affectation des ressources aux activités ;
- Regroupement des inducteurs et le calcul du coût unitaire ;
- Calcul du coût de revient.
Étape 1 : Identification des activités clés de l’entreprise
Bien identifier les activités clés de l'entreprise conditionne la pertinence de la méthode ABC : cette étape est donc cruciale. Elle consiste à identifier quelles étapes du processus de production sont au cœur de consommation des coûts.
Étape 2 : Choix des inducteurs de coûts
Le choix devra se porter sur les inducteurs d’activité et les inducteurs de coûts les plus pertinents pour l’activité considérée. Un inducteur d’activité détermine la quantité des ressources consommées que nécessite chaque produit et donc le coût que cela représente (par exemple, le nombre de commandes pour mesurer l’activité du service achat). Les inducteurs de coûts représentent tous les coûts rattachés à une activité, comme par exemple le nombre d’heures de travail que nécessite l’assemblage des constituants d’un produit. Ils permettent d’estimer les coûts et marges pour chaque référentiel.
Étape 3 : Affectation des ressources aux activités
La méthode ABC prend en compte l'ensemble des charges indirectes liées à l’activité (ressources matérielles, humaines, financières). Ainsi, sont affectées à chacune des activités les ressources qu’elles consomment.
Étape 4 : Regroupement des inducteurs et calcul du coût unitaire
On regroupe ensuite les activités en fonction des inducteurs qu’elles partagent dans ce qu’on appelle des centres de regroupement. Pour chaque centre, on divise la ressource par le nombre d’inducteurs afin de déterminer le coût unitaire.
Étape 5 : Calcul du coût de revient
Le coût de revient est calculé pour chaque centre de regroupement. On l’obtient en additionnant les charges directes et indirectes.
La méthode ABC permet une meilleure gestion des ressources
En logistique, ce travail d’analyse des coûts de revient de chacun des centres de regroupements rend possible des aménagements de l’entrepôt.
- Groupe A : Ce groupe comprend les 20 % des produits qui génèrent à eux seuls 80 % du CA. Le taux de rotation sera donc élevé. Aussi, le réapprovisionnement des ces produits devra être régulier, car s’ils sont en rupture de stock, l'entreprise fera une croix sur une part importante de son CA. De plus, étant donné que ces référentiels sont souvent commandés, il serait judicieux de limiter les déplacements. Par exemple, en les stockant proche du quai de chargement à une hauteur facilement accessible pour les préparateurs de commande.
- Groupe B : Ce groupe comprend 30 % des produits et représente environ 15 % du CA. Ces produits devraient se situer au milieu de l’entrepôt, dans l’attente de se rapprocher du quai s’ils ont du succès ou au contraire d’être relégués au fond de l’entrepôt.
- Groupe C : Les 50 % des articles restants, qui comptent pour 5 % du CA, constituent ce dernier groupe. Ils peuvent être stockés au fond de l’entrepôt car les préparateurs de commande ne devront les collecter que rarement. Ici, la question n’est pas tant « Ces produits sont-ils rentables ? » mais « Est-il rentable de les conserver ? ». En effet, la demande qui les concerne étant erratique, le risque de continuer à les stocker alors qu’ils sont obsolètes est réel. Ainsi, la catégorie C est elle aussi importante, de par la perte d’argent que peut constituer un stockage de produit suranné.
Mais attention : ce n'est pas une raison pour négliger les produits qui entrent dans cette dernière catégorie. Un contretemps à ce niveau engendrerait tout de même des coûts pour l’entreprise dont elle se passerait bien.
Cette disposition optimale des référentiels permettra à la plateforme logistique de gagner en productivité et donc d’être plus compétitif.
Méthode ABC |
|
Quoi |
Méthode d’analyse logistique visant à optimiser les process en se basant sur les coûts à base d’activités. |
Pourquoi |
Gain en productivité qui constitue un avantage concurrentiel. |
Comment |
Classification en 3 types de produits : le groupe A (produit crucial à la rentabilité élevée), le groupe C (rentabilité moindre mais à ne pas négliger pour autant) et le groupe B (produits intermédiaires). |
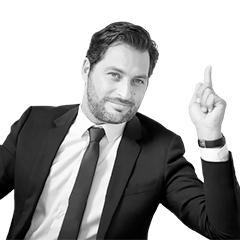
La synthèse de Julien Dupé
(CEO et Fondateur de Infonet.fr)La méthode ABC consiste en l’analyse des coûts à base d’activité de chaque référentiel afin d’identifier lesquelles sont les plus rentables pour l’entreprise. Cela fait, l’agencement des produits s'ajuste en conséquence dans le but d'optimiser la logistique et ainsi gagner en productivité.
Autres définitions de la catégorie Logistique
- Approvisionnement
- Canal de distribution
- Circuit court définition
- Couverture de stock
- Coûts de distribution
- Cross docking
- Crowdsourcing
- Dernier entré, premier sorti
- Délai de livraison
- Entrepôt
- FCO marchandises
- Groupage
- Logistique
- Logistique intégrée
- Pick and Pack
- Premier entré, premier sorti
- Préparateur de commande
- Pyramide du CIM
- Rotation des stocks
- Économie d’échelle