Novadditive propulse la céramique 3D française depuis Tarbes
À Tarbes, Novadditive industrialise l’impression 3D céramique et séduit défense, aéronautique et spatial avec des pièces extrêmes, produites en France.
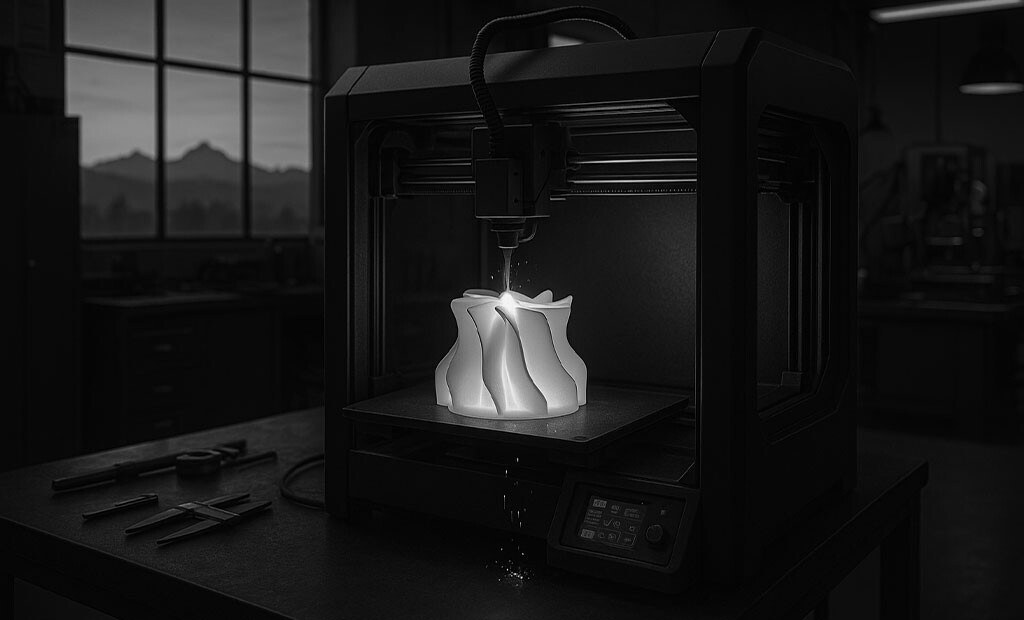
À Tarbes, une PME de quatre personnes construit patiemment l’un des leviers industriels les plus attendus de la décennie : l’impression 3D de céramique technique. L’entreprise Novadditive, mise en lumière le 16 juin 2025 dans le Daily du Salon du Bourget, revendique aujourd’hui la première ligne de production industrielle française dans ce domaine. Voici pourquoi ce discret atelier pyrénéen agite la défense, l’aéronautique, le spatial et le nucléaire.
Le saut technologique que promet la céramique imprimée
Qu’il s’agisse de rotors de turbosoufflantes, d’échangeurs thermiques pour satellites ou de traversées électriques traversant un moteur d’avion, la céramique avancée résiste là où les métaux s’adoucissent. À 2 000 °C, un alliage nickel‑cobalt fatigue ; une alumine dense conserve sa rigidité. Ajouter la liberté géométrique de l’impression 3D revient à combiner la brique réfractaire et la pâte à modeler : on obtient des canaux de refroidissement tortueux, des structures lattices ultralégères, ou encore des pièces monoblocs qui remplacent cinq sous‑ensembles vissés.
Le marché reste jeune : évalué à 270 millions $ en 2023, il pourrait grimper à 2,6 milliards $ d’ici 2032, soit un taux de croissance annuel de 28,6 %. En d’autres termes, la céramique additive passera en dix ans du statut de curiosité de laboratoire à celui de chaîne de valeur pesant autant que l’impression 3D métal en 2018.
Ces matériaux non métalliques et non organiques incluent alumines, nitrures, carbures, zircones, sialons ou composites C/SiC. Ils se distinguent des porcelaines traditionnelles par une porosité quasi nulle, des températures de fusion supérieures à 1 600 °C et des modules d’Young comparables à l’acier.
Un atelier de quatre personnes dans les Hautes‑Pyrénées
Installée au nord de Tarbes, la ligne pilote occupe 450 m² : trois imprimantes steréolithographie (SLA), un système binder jetting maison, une extrudeuse de pâte et trois fours de frittage atteignant 1 750 °C. Le fondateur Vincent Poirier, 35 ans de carrière dans l’ingénierie céramique, a démarré fin 2020 avec ses fonds propres puis a intégré le cluster Primus orienté défense.
La production va du prototype unique à la série de 10 000 noyaux creux pour turbines d’A320 neo. L’entreprise assure également le post‑traitement (ébavurage laser, métrologie par tomographie), ce qui lui évite de sous‑traiter en Allemagne ou aux États‑Unis, les deux places fortes historiques du secteur.
Défense, espace, nucléaire : quatre marchés stratégiques
Défense : buses de guidage de missiles à usage unique ; aéronautique : amenée d’air de chambre de combustion permettant un régime supérieur de 150 °C ; spatial : propulseurs pour cubesats en carbure de silicium très chargé ; nucléaire : gainages isolants résistant aux neutrons rapides. Ces projets ont un dénominateur commun : l’exigence de souveraineté technologique.
Bon à savoir
La France dépend encore à 72 % des importations pour les céramiques de haute performance, contre 38 % pour les alliages nickel (Source Syndicat français des céramiques, 2024).
L’histoire de novadditive : de la silice au composite oxyde‑carbure
Vincent Poirier débute en 1989 sur l’électrophorèse d’implants osseux. Il enchaîne dix-huit ans chez un fabricant de fours à induction, puis rejoint ENS Cachan en tant que chercheur associé sur le frittage flash. En 2017, il découvre la stéréolithographie céramique lors d’un congrès à Vienne et y voit l’occasion de rapatrier un savoir‑faire stratégique. Trois ans plus tard naît Novadditive
L’entreprise détient aujourd’hui cinq contrats pluriannuels : un accord cadre avec un motoriste français, un programme nucléaire de huit ans pour l’CEA et trois lettres d’intention dans le médical (tiges rachidiennes en zircone‑alumine).
Comment fonctionne l’impression 3D céramique ?
SLA céramique : photopolymérisation de résines chargées à 45 % en poudre. Binder jetting : liant pulvérisé sur couches sèches, puis frittage. Extrusion de pâte : fil pré‑cuit poussé par vis. Chaque méthode implique un retrait volumique de 12 à 18 % lors du frittage, que Novadditive compense par une modélisation numérique propriétaire.
1. Préparation du slurry ou de la poudre
2. Impression couche par couche
3. Déliantage thermique pour éliminer polymères ou liant
4. Frittage in vacuo ou sous argon
5. Contrôle par RX ou tomographie.
Finance : quand le participatif rencontre la deep‑tech
En juin 2025, Novadditive a levé 400 000 € auprès de 20 investisseurs via la plateforme SouvTech Invest, dédiée aux industries souveraines. L’objectif : doubler la cadence de production, passer de deux à quatre fours carbographite et recruter un spécialiste HTO (High‑Temperature Oxide) pour sécuriser la qualification aéronautique AC7136.
La levée constitue un signal fort : habituellement, les start‑ups céramiques peinent à attirer des capitaux en raison d’amortissements lourds (>10 ans) et de temps de cycle longs. Or, les restrictions de chaîne d’approvisionnement imposées par la guerre en Ukraine ont redistribué les cartes. Les investisseurs considèrent désormais la capacité à produire localement des biens à double usage comme une barrière stratégique.
Réglementation : double usage, normes et barrières
Les traversées électriques destinées à un turboréacteur militaire relèvent de l’annexe I du règlement UE 2021/821. Toute exportation hors Union nécessite donc une licence du Service des biens à double usage (SBDU). Côté civil, les pièces destinées à des dispositifs médicaux implantables doivent prouver l’absence de plomb et de cadmium selon ISO 6486‑1 révisée en 2023. Novadditive mêle ainsi deux régimes : contrôle défense et réglementation sanitaire, rarement réunies dans la même halle de production.
La start‑up affirme tenir un taux de conformité de 0,3 % de rebut post‑frittage, contre 3 % pour la moyenne européenne (données internes auditées par Bureau Veritas). Cela réduit le coût unitaire malgré une matière première deux fois plus chère qu’un alliage Inconel.
France, allemagne, états‑unis : l’équation de la compétitivité
Si l’on compare trois fournisseurs majeurs — Novadditive (France), Lithoz (Autriche) et CeramTec USA — on observe des écarts de prix acceptables en série 100 pièces : 12 €/cm³ chez Novadditive, 14 €/cm³ à Vienne et 11 €/cm³ en Caroline du Sud. Mais le transport d’une pièce fragile vers Toulouse ou Bordeaux efface en partie l’avantage américain ; l’atout de la proximité logistique devient décisif pour Airbus et Safran.
En R&D, la France arrive néanmoins derrière l’Allemagne : le budget public consacré aux céramiques est estimé à 38 M€ par an, contre 54 M€ outre‑Rhin (VDE Additive Manufacturing Report, 2024).
Perspectives : vers la céramique hybride et la micro‑usine distribuée
Novadditive travaille sur une alumine poreuse infiltrée cuivre pour antennes radar, ainsi que sur un procédé de frittage flash consommant 60 % d’énergie en moins. Le plan 2026–2030 prévoit la licencing de micro‑usines modulaires : un conteneur maritime équipé d’une imprimante, d’un four et d’un laser de découpe pour déployer la production sur un tarmac ou un navire.
La stratégie rappelle celle de certains fabricants d’imprimantes métal qui louent leurs chambres de fusion en conteneurisé. Si le modèle réussit, la souveraineté ne reposera plus sur un site unique, mais sur un réseau d’unités mobiles capables de s’agréger selon les besoins.
Et après ? les pyrennées comme tremplin industriel
L’innovation matérielle se joue rarement sous les ors des capitales ; elle germe souvent là où un savoir‑faire artisanal rencontre une urgence stratégique.