ArcelorMittal : une refonte industrielle qui dynamise l’acier français
ArcelorMittal investit plus de 300 M€ pour moderniser deux sites clé de la sidérurgie française, de Dunkerque à Fos, et renforcer la compétitivité nationale.
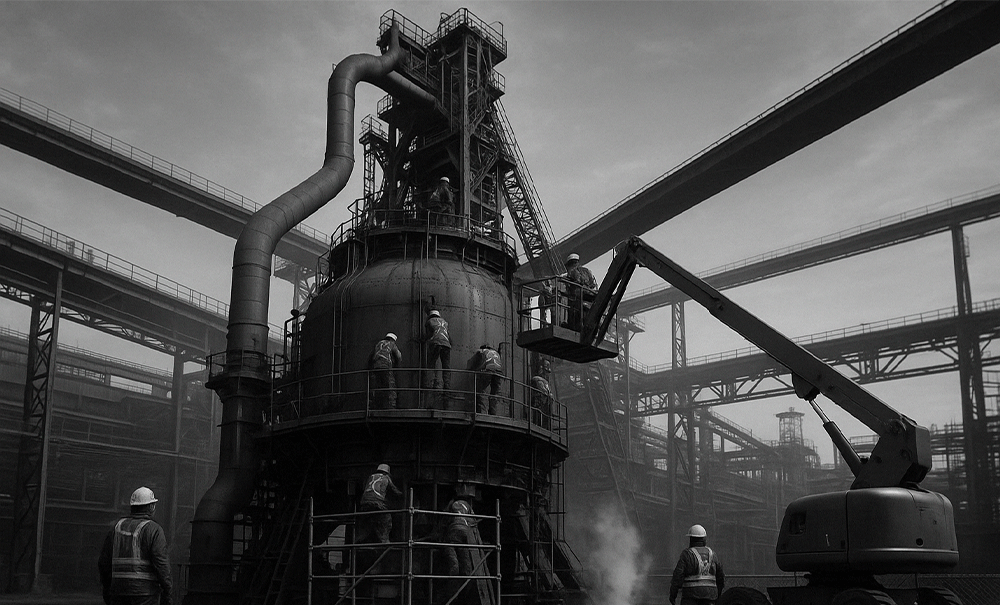
Les hauts-fourneaux français retrouvent la lumière grâce à un programme de maintenance d’envergure, annoncé par ArcelorMittal pour ses sites de Dunkerque et Fos-sur-Mer. Découvrez dans cet article comment ces investissements, estimés à plus de 300 millions d’euros, visent à renforcer la compétitivité sidérurgique et à pérenniser des infrastructures industrielles stratégiques.
Un plan d'investissement majeur pour deux sites stratégiques
Les récents projets dévoilés par ArcelorMittal confirment la volonté du leader mondial de l’acier de garantir la fiabilité et l’efficacité opérationnelle de ses sites français. D’un côté, l’usine de Dunkerque (Nord) va bénéficier d’importants travaux de remise à niveau, notamment sur une chaîne d’agglomération de minerai de fer, le haut-fourneau n°4 et un convertisseur d’aciérie. De l’autre, l’usine de Fos-sur-Mer (Bouches-du-Rhône) s’apprête à rénover le haut-fourneau n°1, essentiel pour maintenir sa capacité de production.
Ce plan d’envergure, estimé à plus de 300 millions d’euros, se décompose en 254 millions pour le site dunkerquois et 53 millions pour l’usine méridionale. Au-delà du montant, la portée de ce chantier réside dans la sécurisation de l’outil industriel français, souvent mis à l’épreuve par une conjoncture internationale volatile. Grâce à cette enveloppe, les deux sites renforceront leur position au sein du marché européen de l’acier, tout en anticipant les futurs défis économiques.
Pour les observateurs avisés, cet investissement n’est pas anecdotique : il illustre la façon dont ArcelorMittal, malgré une concurrence féroce et les évolutions du marché mondial, s’attache à pérenniser ses capacités de production en France. Dans un contexte où la compétitivité est le maître-mot, cette enveloppe constitue un signal fort envoyé tant aux salariés qu’aux acteurs institutionnels.
Bon à savoir : Les principaux postes de dépense
Dans ce type de chantier, la majeure partie de l’investissement concerne la modernisation d’équipements stratégiques (haut-fourneaux, convertisseurs, installations de traitement). Les sommes restantes couvrent la logistique, la sécurité, la formation du personnel et l’anticipation d’éventuelles hausses de coûts liées au marché des matières premières.
Le site de Dunkerque : maintenir la performance industrielle
Le site de Dunkerque fait figure de pilier historique dans le paysage sidérurgique français. Ses équipements sont dimensionnés pour produire chaque année un volume considérable d’acier primaire, destiné ensuite à des filières variées (automobile, construction, emballage, etc.). Or, pour préserver la compétitivité de cette usine, une maintenance régulière est indispensable.
Au deuxième trimestre de cette année, trois installations clés sont visées : une chaîne d’agglomération, le haut-fourneau numéro 4 et l’un des convertisseurs de l’aciérie. Les équipes locales, mobilisées depuis plus d’un an pour planifier chaque étape, redoublent d’efforts afin d’optimiser la durée d’arrêt des outils et de limiter l’impact sur l’ensemble de la chaîne.
Une partie de ces travaux implique un arrêt de 90 jours du haut-fourneau n°4. C’est un moment charnière pour les ingénieurs, qui doivent coordonner le démontage, la réfection et la remise en service de manière à éviter tout goulot d’étranglement dans l’alimentation des lignes de production en aval. Les enjeux logistiques sont donc multiples : de l’approvisionnement en matières premières à la distribution des produits finis, chaque maillon de la chaîne se retrouve sous la loupe.
Un haut-fourneau est une installation industrielle où l’on produit de la fonte à partir du minerai de fer et du coke. Cette fonte est ensuite transformée en acier dans les convertisseurs. La maintenance de ces infrastructures impose des temps d’arrêt importants, car la réfection intérieure (revêtement, réfractaires, etc.) exige une mise au repos et un refroidissement progressif de l’ensemble.
Le coût total de 254 millions d’euros sur Dunkerque se justifie par l’ampleur des pièces à remplacer, la technicité requise et la nécessité de respecter des normes sécuritaires strictes. En outre, des études préalables ont dû être menées pour identifier précisément les zones les plus sensibles et programmer ainsi chaque chantier dans l’ordre le plus efficace.
Rappelons que la production d’acier primaire est particulièrement exigeante sur le plan énergétique. Par conséquent, la remise en état d’un haut-fourneau permet non seulement de pérenniser l’outil de travail, mais aussi d’améliorer potentiellement l’efficacité énergétique, un paramètre de plus en plus crucial au vu des tensions sur le marché de l’énergie.
ArcelorMittal s’appuie sur des collaborateurs spécialisés en métallurgie, en ingénierie et en maintenance industrielle. Régulièrement formés aux dernières techniques, ils veillent à optimiser les interventions pour limiter l’impact sur la production et garantir une remise en service dans les délais prévus.
Focus sur le haut-fourneau numéro 4
Le haut-fourneau numéro 4 de Dunkerque occupe une place prépondérante dans la stratégie de production. Construit pour satisfaire une demande d’acier toujours croissante, il est soumis à de fortes contraintes thermiques et mécaniques. Une révision complète de ses composants internes est donc cruciale pour prolonger sa durée de vie et préserver la qualité de la fonte produite.
L’arrêt programmé à 90 jours n’est pas décidé à la légère. Les professionnels chargés de la maintenance doivent démonter et inspecter chaque segment, du creuset jusqu’au gueulard, en passant par les systèmes de refroidissement. L’expérience acquise sur les précédents entretiens de ce type facilite la planification, mais chaque intervention reste un défi en soi, compte tenu du caractère unique de l’installation.
De plus, cette remise à neuf s’accompagne souvent de mises à niveau technologiques. Les haut-fourneaux modernes se dotent parfois d’instruments de mesure plus précis, ou de revêtements réfractaires plus performants, capables de contenir des températures extrêmes tout en réduisant les pertes énergétiques. Ainsi, l’objectif ne se limite pas à maintenir la capacité de production : il s’agit également d’anticiper les évolutions du marché et de rester compétitif sur le long terme.
Bon à savoir : la durée de vie d’un haut-fourneau
En règle générale, la durée de fonctionnement optimal d’un haut-fourneau s’étend entre 15 et 20 ans avant de nécessiter une rénovation majeure. Chaque révision permet de prolonger d’autant la capacité opérationnelle, si elle est menée correctement et si les contrôles réguliers sont respectés.
Sur le plan économique, ce genre d’arrêt prolongé représente un manque à gagner temporaire pour l’entreprise. Toutefois, il est compensé par la réduction des risques de pannes imprévues et le gain en performance une fois l’installation rouverte. De plus, ArcelorMittal anticipe ces périodes afin de sécuriser l’approvisionnement en acier pour ses clients, évitant ainsi d’impacter trop lourdement le marché.
Le défi logistique et les impacts sur la chaîne de production
Outre la partie technique, la phase de maintenance du site de Dunkerque requiert une planification logistique très minutieuse. Pendant l’arrêt du haut-fourneau n°4, les autres installations doivent maintenir un rythme satisfaisant pour honorer les commandes, notamment en aval, où se situent les lignes de laminage et de transformation de l’acier.
Les approvisionnements en minerai de fer, en coke et autres matières premières ne doivent pas s’accumuler ou créer un surstockage inutile. Au contraire, un juste équilibre est recherché pour que les flux restent cohérents avec la baisse temporaire de capacité. Les équipes en charge de la supply chain travaillent main dans la main avec la production, afin de lisser les variations et d’éviter tout goulot d’étranglement.
Bon à savoir : flux tendus vs flux stockés
Dans l’industrie sidérurgique, on privilégie souvent des flux tendus pour minimiser les coûts de stockage. Toutefois, lorsque des maintenances exceptionnelles sont prévues, il peut être nécessaire de constituer un petit stock tampon pour satisfaire la demande des clients pendant l’arrêt de l’installation clé.
Du point de vue social, la coordination entre les équipes internes et les sous-traitants mobilisés sur le chantier représente un second enjeu. Le site de Dunkerque reste l’un des plus importants employeurs de la région, et tout arrêt massif peut susciter des interrogations chez les salariés comme chez les riverains. En l’occurrence, la direction assure que les mesures de continuité sont en place pour éviter un arrêt complet de la production.
L’impact sur l’emploi local peut, en réalité, être positif à court terme, puisqu’un grand nombre de prestataires spécialisés sera mobilisé pour des opérations techniques pointues. Sur le moyen et long terme, la mise à niveau des installations renforce la pérennité du site, et donc la sécurité des emplois existants, dans un secteur souvent confronté à des ajustements de capacités.
La maintenance préventive permet d’anticiper les pannes grâce à des inspections régulières et des remplacements planifiés de pièces d’usure. Cela évite des arrêts en urgence qui peuvent coûter cher à l’entreprise et perturber de façon imprévisible la chaîne de production.
Fos-sur-Mer : rénover pour assurer l’avenir
En parallèle de Dunkerque, le site de Fos-sur-Mer bénéficiera d’une enveloppe de 53 millions d’euros destinée au haut-fourneau n°1. Cette unité, dont la durée de vie doit être prolongée, sera rénovée en profondeur afin d’assurer un niveau de production stable et de sécuriser l’avenir du site.
Le calendrier prévisionnel table sur un redémarrage au cours du premier semestre 2026. Il se fera en relais du haut-fourneau n°2, actuellement en fonctionnement, pour éviter que le site ne tourne sur deux lignes majeures en même temps, ce qui serait en contradiction avec la stratégie industrielle annoncée à l’été 2024. En effet, ArcelorMittal avait alors déclaré vouloir adopter une marche durable avec un seul haut-fourneau, compte tenu d’un contexte économique plus tendu.
Le haut-fourneau n°1 est un élément clé de la capacité sidérurgique de Fos-sur-Mer. Situé à proximité du port de Marseille, ce site jouit d’un positionnement géographique avantageux pour l’importation de matières premières et l’exportation d’acier. Cependant, pour maintenir cette attractivité, l’installation doit être à la pointe sur les plans technologique et environnemental. Ces travaux de maintenance sont donc l’occasion d’intégrer des innovations permettant de réduire la consommation d’énergie et d’améliorer la qualité des effluents.
Du point de vue local, l’usinage et la transformation de l’acier à Fos-sur-Mer s’inscrivent dans un bassin industriel dense, englobant la pétrochimie et la logistique portuaire. L’enjeu est de faire en sorte que la sidérurgie continue de jouer un rôle moteur dans cette dynamique, tout en s’adaptant aux pressions réglementaires croissantes (émissions de CO₂, rejets atmosphériques, etc.).
Perspectives économiques et enjeux financiers
Si la maintenance de Dunkerque et Fos-sur-Mer apparaît comme une nécessité technique, elle soulève aussi des questions d’ordre économique. Dans un marché mondial de l’acier soumis à des fluctuations de prix, ArcelorMittal doit composer avec la concurrence de régions où les coûts de production sont souvent plus faibles (Asie, pays émergents).
Cet investissement de plus de 300 millions d’euros intervient à une période où la demande reste incertaine en Europe, dans un contexte de croissance ralentie. D’un côté, il constitue un signal fort sur la volonté de l’entreprise de maintenir des sites en France. De l’autre, il exige un retour sur investissement sur plusieurs années, alors que les marges dans la sidérurgie peuvent être volatiles.
Sur le plan financier, la stratégie d’ArcelorMittal s’articule autour de la préservation de sa part de marché en Europe, tout en consolidant ses positions internationales. En multipliant les initiatives de modernisation, le groupe cherche à gagner en compétitivité pour limiter l’impact de la pression concurrentielle. Ainsi, ces travaux participent à la logique plus large de rationalisation et d’optimisation des sites du groupe.
Le recours possible à des aides ou incitations publiques peut aussi peser dans la balance. L’État français, attentif au maintien de la filière sidérurgique, a parfois soutenu des projets de ce type par des dispositifs d’accompagnement financier ou via des partenariats de recherche (en particulier autour de la décarbonation). Dans ce cadre, ArcelorMittal pourrait bénéficier d’un environnement plus favorable pour pérenniser ses activités sur le territoire.
Qui est ArcelorMittal ?
Fruit de la fusion entre Arcelor et Mittal Steel en 2006, ArcelorMittal est devenu le numéro un mondial de la sidérurgie, avec des implantations sur les cinq continents. Le groupe produit de l’acier pour des secteurs variés, allant de l’automobile à la construction, en passant par l’électroménager et les emballages. Son chiffre d’affaires se chiffre en dizaines de milliards d’euros chaque année.
En France, ArcelorMittal est un acteur industriel majeur, héritier de l’histoire sidérurgique lorraine, du Nord et du littoral méditerranéen. Le site de Dunkerque, en particulier, symbolise la puissance industrielle du groupe, tandis que Fos-sur-Mer bénéficie d’une situation géographique avantageuse pour les échanges commerciaux. Malgré des périodes de restructuration et de fermeture de certains sites, le groupe conserve une empreinte significative.
D’un point de vue stratégique, ArcelorMittal mise sur l’innovation et la modernisation pour rester un leader mondial. Les enjeux actuels portent notamment sur la réduction de l’empreinte carbone, la transformation numérique des processus industriels (Industrie 4.0) et la compétitivité face aux sidérurgistes asiatiques. Les opérations de maintenance à Dunkerque et Fos-sur-Mer s’inscrivent dans cette logique de long terme.
En outre, l’entreprise s’est engagée dans plusieurs projets de recherche et développement, particulièrement en Europe, où se trouvent certaines de ses installations les plus avancées. L’objectif : inventer des procédés de fabrication plus durables, tout en garantissant une production à grande échelle. Les investissements récents dans la maintenance illustrent aussi la volonté du groupe de ne pas délocaliser certaines activités critiques, mais plutôt de les pérenniser sur le sol français.
Aspects réglementaires et environnementaux
La sidérurgie est l’un des secteurs les plus réglementés en matière d’environnement, en raison de sa consommation énergétique et de ses émissions de gaz à effet de serre. En investissant dans la rénovation de ses installations, ArcelorMittal répond non seulement à des impératifs industriels, mais s’aligne également sur les normes françaises et européennes de plus en plus exigeantes.
À Dunkerque comme à Fos-sur-Mer, la remise en état des hauts-fourneaux inclura vraisemblablement des améliorations visant à réduire l’empreinte écologique. Par exemple, des filtres plus performants peuvent être installés pour limiter les rejets polluants. De même, la mise à jour des systèmes de récupération de chaleur contribue à diminuer la consommation d’énergie globale.
Ces efforts sont d’autant plus importants que l’Union européenne, dans le cadre de son pacte vert, encourage une décarbonation rapide des secteurs industriels lourds. Les industriels sidérurgiques, soumis au système d’échange de quotas d’émission (ETS), doivent donc trouver un équilibre entre compétitivité et adaptation aux enjeux climatiques.
Pour ArcelorMittal, investir dans des projets de maintenance haut de gamme peut aussi servir de vitrine pour démontrer sa capacité à innover sur le plan environnemental. Les différentes directions d’usine sont ainsi encouragées à intégrer des objectifs de performance énergétique et de réduction des rejets lors de la phase de conception du chantier.
De multiples défis pour la filière sidérurgique française
La situation de la sidérurgie en France n’est pas isolée de ce qui se passe à l’échelle mondiale. Les défis sont multiples : pression concurrentielle, volatilité des prix des matières premières, évolution de la demande, transition écologique et mutations technologiques. Malgré tout, le pays dispose encore de sites stratégiques comme Dunkerque et Fos-sur-Mer, qui permettent de soutenir la production nationale.
Le choix d’ArcelorMittal d’y investir témoigne d’une certaine confiance dans la capacité de la France à demeurer compétitive. Toutefois, l’avenir de la filière dépend aussi des politiques publiques, de l’évolution des coûts de l’énergie et de la réactivité du marché intérieur. De même, la capacité à intégrer les nouvelles technologies (intelligence artificielle, automatisation, etc.) jouera un rôle majeur pour optimiser les procédés et réduire la dépendance énergétique.
Les organisations professionnelles, comme la Fédération Française de l’Acier, se félicitent généralement de ce type de projet, car il limite la tentation de délocaliser la production vers des zones où la main-d’œuvre est moins coûteuse. En parallèle, les syndicats de salariés y voient une opportunité de sécuriser l’emploi local, à condition que ces travaux s’accompagnent de plans de formation et d’amélioration des conditions de travail.
L’une des interrogations majeures pour les prochaines années concerne la capacité du secteur à se transformer en profondeur : produire un acier plus vert, mettre en place une économie circulaire (recyclage de la ferraille, valorisation des sous-produits, etc.) et intégrer des processus innovants comme l’hydrogène décarboné pour remplacer partiellement le coke. Les investissements de maintenance actuels, s’ils intègrent cette perspective, pourraient jeter les bases d’une refonte plus profonde à moyen terme.
Regard sur la durée de vie des installations
Les outils industriels de la sidérurgie sont particulièrement coûteux à construire et à entretenir. Un haut-fourneau, par exemple, nécessite des investissements initiaux colossaux et génère des frais d’exploitation importants (main-d’œuvre, énergie, matières premières). En contrepartie, lorsqu’il fonctionne à plein régime, il offre une grande capacité de production pour répondre à une demande soutenue.
La durée de vie d’une installation est généralement prolongée par des opérations de maintenance lourde menées à intervalles réguliers. À chaque arrêt, les ingénieurs cherchent à accroître l’efficacité énergétique et la productivité, tout en réduisant les coûts de maintenance futurs. C’est un cercle vertueux : plus l’outil est fiable, plus il rapporte, et plus il devient rentable d’investir pour le maintenir à jour.
Néanmoins, le contexte économique peut parfois pousser les groupes sidérurgiques à retarder certains travaux coûteux, voire à mettre sous cocon (arrêt prolongé) un haut-fourneau si la demande se contracte. Dans le cas de Dunkerque et Fos-sur-Mer, le choix d’investir massivement dès maintenant illustre la volonté de conserver un potentiel de production élevé en France, pour ne pas se retrouver démuni lorsque la demande repartira.
En outre, la dynamique industrielle locale peut influencer la rentabilité à long terme. Un site comme Dunkerque peut compter sur une main-d’œuvre qualifiée, un écosystème industriel solide et des infrastructures portuaires de premier plan. Fos-sur-Mer, quant à lui, bénéficie de la proximité du port de Marseille, facilitant l’import/export. Ces atouts justifient, en partie, la décision d’ArcelorMittal de poursuivre l’aventure.
Une ambition sur la productivité et la compétitivité
Dans la sidérurgie, la productivité se mesure à la fois par la quantité d’acier produite et par la maîtrise des coûts de revient. Chaque opération de maintenance vise à augmenter la productivité en améliorant la fiabilité des équipements et en réduisant les pertes liées aux arrêts non planifiés.
En investissant 254 millions d’euros à Dunkerque et 53 millions d’euros à Fos-sur-Mer, ArcelorMittal espère accélérer le retour de ses capitaux investis grâce à une performance opérationnelle accrue. Pour rester compétitif, le groupe doit maintenir un coût unitaire de production plus bas que ses principaux concurrents européens et internationaux.
La compétitivité de ces deux sites passe également par le maintien de normes de qualité strictes, répondant aux besoins exigeants de secteurs comme l’automobile. En modernisant ses outils de production, l’entreprise est en mesure de livrer un acier aux propriétés mécaniques plus constantes, tout en respectant des délais de livraison serrés.
Par ailleurs, la compétitivité ne se limite pas à l’aspect coût : la fiabilité des approvisionnements, la proximité avec les clients finaux et la réactivité en cas de fluctuations de la demande constituent autant de facteurs déterminants. Les investissements de maintenance améliorent ces paramètres, en réduisant la probabilité de pannes et en assurant une meilleure planification des flux.
Investir face à la volatilité du marché mondial
Le marché mondial de l’acier connaît des soubresauts réguliers, liés notamment à la conjoncture économique, aux tensions commerciales et à la variation des prix des matières premières. Dans ce contexte incertain, ArcelorMittal fait le choix d’investir en France plutôt que de concentrer ses efforts sur d’autres zones de production peut-être moins coûteuses.
Ce parti pris souligne l’importance stratégique du marché européen et la volonté de disposer d’installations compétitives sur le Vieux Continent. Lorsque la demande mondiale est en berne, les sites qui affichent les meilleurs rendements sont généralement préservés, tandis que les moins rentables risquent la fermeture ou la mise sous cocon. Dunkerque et Fos-sur-Mer ont donc tout intérêt à rester au sommet de leur forme industrielle.
Pour justifier cet engagement sur le long terme, le groupe se base sur des prévisions qui, malgré leur incertitude, laissent entrevoir une reprise progressive de la demande d’acier en Europe. Les secteurs de la construction et de l’automobile, bien que chahutés, devraient continuer à nécessiter des volumes élevés. Quant aux industries de niche (éolien, ferroviaire, emballage écologique), elles offrent aussi des opportunités de croissance.
En parallèle, la volatilité du marché impose une gestion rigoureuse des coûts. Les chantiers de maintenance se doivent d’être achevés dans les délais et budgets impartis. Tout dépassement important pourrait peser sur la rentabilité du projet. Les équipes en charge de piloter ces travaux doivent donc faire preuve d’un grand professionnalisme pour allier rigueur, qualité et maîtrise des dépenses.
ArcelorMittal et la transition énergétique
La transition énergétique est devenue un enjeu capital pour les industriels, et la sidérurgie ne fait pas exception. Les hauts-fourneaux sont souvent pointés du doigt pour leur intensité carbone, liée à l’emploi du coke comme agent réducteur. Cependant, ArcelorMittal multiplie les projets pilotes pour réduire ces émissions, en substituant par exemple une partie du coke par des biomasses ou de l’hydrogène vert.
Si la maintenance en cours n’a pas pour objet principal de transformer radicalement la technologie du haut-fourneau, elle pourrait tout de même inclure des améliorations tangibles pour réduire les consommations d’énergie et les pertes thermiques. À long terme, la modernisation régulière des installations offrira plus de flexibilité pour intégrer ces nouvelles méthodes de production plus vertueuses.
Par ailleurs, la place de l’acier dans la transition énergétique est souvent sous-estimée. Utilisé dans les éoliennes, les panneaux solaires, les infrastructures de transport électrique ou les véhicules peu émetteurs, l’acier reste un matériau indispensable pour construire les solutions de demain. En sécurisant son outil industriel en France, ArcelorMittal s’assure de pouvoir fournir des aciers performants pour ces marchés émergents.
Bien sûr, la route vers la décarbonation totale est encore longue. Les industriels de l’acier doivent composer avec des process historiques, ancrés dans une tradition de plusieurs décennies, et qui ne se modifient pas du jour au lendemain. Les investissements de maintenance servent donc à préparer cette transition, en rendant les hauts-fourneaux plus adaptables aux technologies futures.
Quand la maintenance rime avec innovation
Dans l’imaginaire collectif, la maintenance renvoie parfois à de simples opérations de remplacement de pièces usées. Or, dans le secteur sidérurgique, chaque arrêt programmé est une opportunité pour repenser l’équipement et intégrer des innovations. Cela concerne aussi bien la surveillance numérique des installations que l’automatisation de certaines tâches.
Par exemple, la réfection d’un haut-fourneau peut s’accompagner de l’installation de capteurs IoT (Internet of Things) qui permettent de collecter en temps réel des données sur la température, la pression ou le flux de matières. Ces informations sont ensuite analysées grâce à des algorithmes afin de détecter plus vite les anomalies et optimiser la consommation énergétique.
Autre exemple : l’automatisation de certains procédés logistiques, comme l’acheminement du minerai ou le chargement des wagons, permet de réduire les coûts opérationnels et d’améliorer la sécurité du personnel. Les chantiers de maintenance constituent un moment idéal pour intégrer ces nouvelles fonctionnalités, car ils impliquent déjà l’arrêt partiel ou total de la chaîne de production.
À terme, l’usine intelligente devient une réalité, et ArcelorMittal entend jouer un rôle de premier plan dans cette transformation. Les gains de productivité et de compétitivité qui en découlent pourraient permettre à la sidérurgie française de se distinguer dans un secteur mondial de plus en plus concurrentiel. Les travaux actuels à Dunkerque et Fos-sur-Mer serviront donc de laboratoires grandeur nature pour tester certaines solutions novatrices.
Une dynamique industrielle au bénéfice des régions
L’impact d’un tel investissement dépasse largement le seul périmètre de l’usine. À Dunkerque, l’activité induite par les chantiers de maintenance profite au tissu économique local : hôtellerie, restauration, commerce, transport, etc. De même, à Fos-sur-Mer, la venue de sous-traitants spécialisés et d’équipements de pointe contribue à dynamiser l’économie régionale.
Au-delà des retombées immédiates, la pérennité de l’activité sidérurgique garantit une stabilité sociale précieuse dans des bassins souvent marqués par les mutations industrielles. Les collectivités locales accompagnent ces projets et y voient un signal positif, confirmant la volonté d’ArcelorMittal de consolider l’emploi sur le territoire.
La formation professionnelle n’est pas en reste. Pour mener à bien les opérations de maintenance, il faut du personnel formé à des métiers techniques très spécifiques : chaudronnerie, soudure, instrumentation, automatisation, etc. Les centres de formation et les écoles d’ingénieurs locales peuvent ainsi s’associer au projet afin de proposer des cursus adaptés aux besoins du chantier.
D’un point de vue plus large, l’amélioration de la compétitivité des sites français de ArcelorMittal renforce l’image d’une France industrielle capable d’innover et de soutenir des projets d’envergure internationale. Dans un climat parfois morose, ce genre d’initiative redonne confiance aux acteurs économiques et témoigne d’une certaine résilience face aux aléas de la mondialisation.
La réflexion finale sur l’avenir du groupe
À travers ces chantiers de maintenance, ArcelorMittal réaffirme son ancrage dans l’Hexagone et son ambition de maintenir une sidérurgie de pointe, compétitive et responsable. L’investissement de plus de 300 millions d’euros entre Dunkerque et Fos-sur-Mer confirme la dimension stratégique de la France pour le premier producteur mondial d’acier. Les bénéfices attendus se situent à plusieurs niveaux : fiabilité, compétitivité, image de marque et perspectives pour l’emploi local.
Il est cependant trop tôt pour mesurer toutes les retombées économiques à long terme. La sidérurgie demeure un secteur cyclique, tributaire des fluctuations de la conjoncture internationale. Mais en modernisant régulièrement ses installations, ArcelorMittal se dote d’un atout solide pour aborder les prochaines années avec sérénité et répondre aux défis de la transition écologique.
Ces opérations de maintenance dépassent le simple enjeu technique : elles illustrent la volonté d’un géant de l’acier de rester à l’avant-garde, de préserver des savoir-faire locaux et de préparer activement un futur marqué par l’innovation et la responsabilité environnementale.