Le Groupe Renault et Atos lancent un service pour collecter des datas de fabrication à grande échelle
Renault et Atos s'allient pour créer un service de collecte de données industrielles afin d'accompagner les entreprises vers la numérisation de l'induustrie.
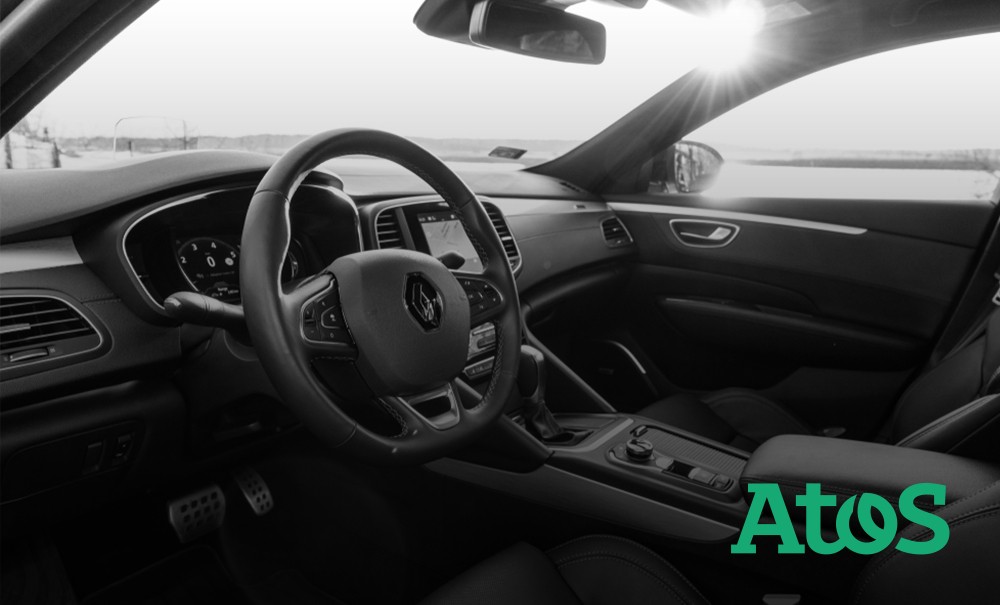
Le groupe Renault et Atos se lancent dans un nouveau service de collecte de données industrielles dans le but d'accompagner les entreprises manufacturières. Il s'agit d'une nouvelle étape vers la numérisation de l'industrie en améliorant la performance opérationnelle des équipements de fabrication : un soutien pour permettre une productivité plus élevée, moins de défauts et une consommation d'énergie plus faible.
Un service de collecte de données industrielles
Le Groupe Renault et Atos lancent ID@S (Industrial Data at Scale), un nouveau service de collecte de données industrielles pour accompagner les entreprises manufacturières dans leur parcours numérique vers l'industrie 4.0. ID@S permettra aux fabricants de collecter et de structurer les données des équipements industriels à grande échelle afin d'améliorer l'excellence opérationnelle et la qualité des produits. Développé par le constructeur automobile et déjà en service dans ses usines, ID@S est désormais industrialisé, modularisé et commercialisé par le leader du numérique Atos.
Tout au long du processus de production, les fabricants génèrent une quantité incroyable de données. Dans la plupart des cas, les données sont sous-exploitées, en raison de leur diversité, du manque de normalisation et du temps d'exploitation. Avec la mise en œuvre d'ID@S, les fabricants seront désormais en mesure de collecter des données provenant d'un large éventail d'équipements industriels (divers fournisseurs, générations, localisation mondiale, mises à jour de micrologiciels, etc.) de manière standardisée et efficace, puis de les contextualiser et de les rendre disponibles dans le cloud. De cette façon, les données corrigent et étendent les processus de production et la qualité des produits avec un effet immédiat. En outre, avec ID@S, les fabricants peuvent surveiller et optimiser l'énergie consommée sur les lignes de production.
Une solution déjà adoptée
Dans le cadre de la stratégie de transformation numérique de l'entreprise, les équipes informatiques, numériques et d'ingénierie du Groupe Renault ont développé cette solution pour capturer les données de ses sites de production. Pour chaque type de processus de fabrication, les données sont collectées et structurées de manière standardisée, ce qui permet d'aborder une variété de cas d'utilisation dans les domaines de la fabrication, de l'ingénierie, de la qualité, de la RSE, de la logistique, etc. Aujourd'hui, cette solution est déployée à grande échelle sur vingt-deux sites du groupe Renault.
Plus de 7 500 équipements sont connectés, avec des modèles de données standardisés représentant plus de 50 processus de fabrication différents, du boulonnage à l'injection d'aluminium, en passant par le soudage, l'usinage, la peinture et l'emboutissage du châssis de la voiture, ainsi que de nouveaux processus de fabrication de moteurs électriques et de batteries. Le Groupe Renault économise déjà 80 millions d'euros par an et entend déployer cette solution dans le reste de ses 35 usines, en connectant plus de 22 000 équipements, d'ici à 2023 pour générer des économies de 200 millions d'euros par an.