Dassault Systèmes et Airbus : nouvelle ère numérique pour l’aviation
L’alliance stratégique propulse la 3DEXPERIENCE au cœur de l’aéronautique, optimisant la conception, la production et la maintenance pour Airbus.
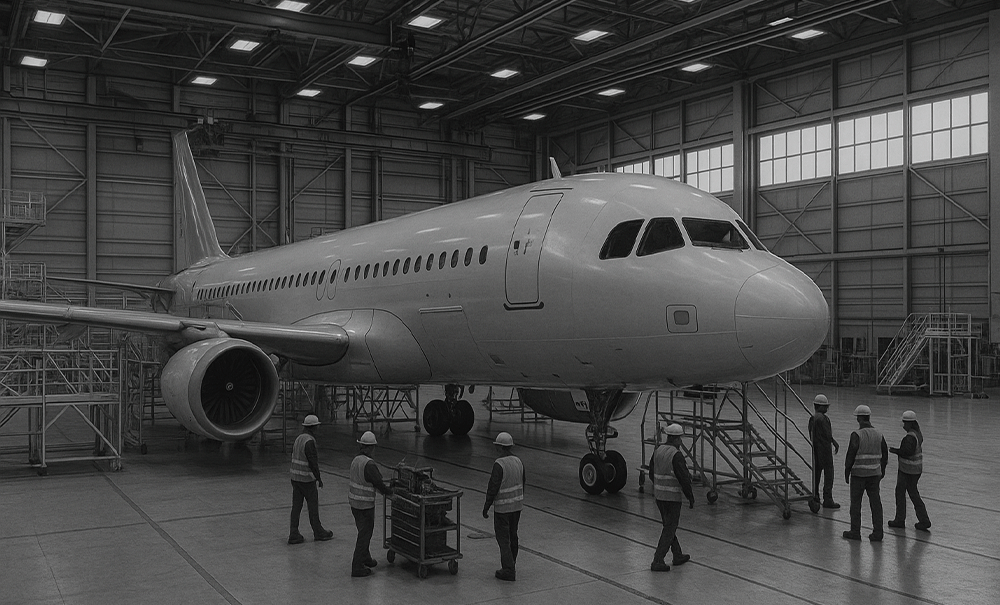
Bienvenue sur notre couverture approfondie d’un nouvel accord stratégique majeur dans l’industrie aéronautique. Le partenariat entre Dassault Systèmes et Airbus gagne en ampleur, avec la volonté de construire l’avenir des avions civils et militaires grâce à la technologie des jumeaux virtuels et à l’usage intensif de la plateforme 3DEXPERIENCE. Voici un décryptage complet, agrémenté d’analyses et de repères pour mieux cerner les enjeux de cette alliance qui, selon les informations communiquées, va mobiliser plus de 20 000 utilisateurs et transformer la façon dont sont conçus, produits et maintenus les futurs appareils.
Une alliance forgée par la volonté d’innover
Des accords entre Airbus et Dassault Systèmes existent de longue date, mais ce nouveau chapitre marque une intensification sans précédent de leur coopération. Au-delà d’une simple mutualisation de compétences, il s’agit d’un véritable virage stratégique. Airbus, géant européen de l’aéronautique, ambitionne d’optimiser tous ses programmes civils et militaires. Quant à Dassault Systèmes, l’éditeur de logiciels dont le siège est basé à Vélizy-Villacoublay, il met à disposition son savoir-faire dans la création de mondes virtuels au service de la vie réelle.
Le contrat signé le 24 avril 2025 établit que les processus de développement, de production et de gestion de la flotte Airbus s’articuleront autour de la plateforme 3DEXPERIENCE. Cet écosystème numérique consolide toutes les étapes du cycle de vie d’un produit, de la conception à l’après-vente, en passant par l’industrialisation. Il va donc impacter largement la chaîne d’approvisionnement, poussant l’ensemble des partenaires, y compris les fournisseurs, à adopter une approche collaborative et connectée.
La 3DEXPERIENCE : un accélérateur pour la performance
La 3DEXPERIENCE est souvent décrite comme un environnement numérique unifié, englobant la conception assistée par ordinateur (CAO), la simulation, la gestion des données et la collaboration en temps réel. L’idée est de pouvoir modéliser un produit dans toutes ses dimensions, depuis l’instant où il est imaginé jusqu’à celui où il sera démantelé ou recyclé. Dans le contexte aéronautique, cette approche permet de créer et d’exploiter des jumeaux virtuels capables d’intégrer des données issues de multiples sources – production, maintenance, retours d’expérience des pilotes, etc.
Pour Airbus, l’enjeu est de taille : réduire les cycles de développement, améliorer le contrôle des coûts et anticiper les besoins industriels. Afin d’augmenter la cadence de sortie de ses appareils, il est indispensable que la transition entre les différentes étapes de la chaîne de production se fasse plus rapidement et avec moins d’aléas. C’est là que le jumeau virtuel apporte une valeur ajoutée : il simule des scénarios complexes et teste virtuellement l’ensemble des fonctionnalités avant de lancer la fabrication réelle.
Le jumeau virtuel est une réplique numérique d’un objet physique ou d’un système complexe. Il intègre des données en temps réel et permet de simuler différents scénarios, afin de repérer et résoudre des problèmes potentiels avant de les rencontrer dans la réalité.
Numérisation et souveraineté : la stratégie du cloud en France
Le choix d’un cloud souverain est un aspect souvent peu médiatisé, mais crucial dans ce type d’accord. Airbus, tout comme Dassault Systèmes, s’engage à ce que les données sensibles ne quittent pas l’espace européen, conformément aux exigences de sécurité et de souveraineté numérique. Dans un secteur stratégique comme l’aéronautique, la protection des informations classifiées revêt une importance capitale. Ce dispositif garantit donc que le transfert et le stockage des données se feront sous juridiction française ou européenne, à l’abri des regards indiscrets.
Pour Dassault Systèmes, cela implique de proposer des solutions cloud adaptées, robustes et conformes aux normes internationales de cybersécurité. Cette approche rassure non seulement Airbus, mais aussi tous les autres acteurs de l’écosystème (sous-traitants, laboratoires, instituts de recherche…), qui souhaitent profiter de la puissance de calcul distribuée sans craindre une fuite de données ou un accès non autorisé.
Au cœur de la chaîne de valeur : 20 000 utilisateurs mobilisés
Le nombre annoncé de 20 000 utilisateurs est considérable. Il ne s’agit pas seulement d’employés Airbus, mais également de partenaires extérieurs et de fournisseurs qui seront amenés à utiliser les mêmes outils numériques. Cette mutualisation informatique casse les silos et promet une collaboration plus fluide : chacun bénéficie d’une vision actualisée en temps réel, tandis que la direction peut suivre l’état d’avancement des projets avec une précision accrue.
Du dessin initial au service après-vente, l’information circule de manière transversale et en continu. Cela accélère la prise de décision, évite les doublons et réduit les écarts éventuels entre ce qui est conçu dans le bureau d’études et ce qui est finalement produit sur la ligne d’assemblage. Une telle transversalité est déjà pratiquée dans d’autres industries, mais son intensification dans l’aéronautique témoigne d’une transformation numérique majeure.
Bon à savoir : un enjeu pour la formation du personnel
La modernisation des processus implique également de former des milliers de professionnels à la maîtrise de la plateforme 3DEXPERIENCE. Les départements RH d’Airbus et de ses partenaires devront déployer des programmes de montée en compétences pour assurer une transition fluide.
En quoi ce partenariat s’inscrit-il dans un contexte plus large ?
Le secteur aéronautique européen, dans son ensemble, fait face à des défis sans précédent. Les objectifs de décarbonation, la course à la compétitivité face aux acteurs américains et asiatiques, ainsi que l’évolution des besoins en défense façonnent les priorités. Pour Airbus, l’augmentation des cadences de production d’avions commerciaux doit se faire sans compromettre la qualité ni la fiabilité. D’autre part, la recherche de nouveaux concepts d’avions moins polluants implique une innovation constante, tant sur les motorisations que sur l’architecture des appareils.
Dans ce tableau, la rationalisation des coûts est capitale. En exploiter davantage sur la puissance du numérique semble indispensable pour maintenir une compétitivité internationale. Le partenariat renouvelé avec Dassault Systèmes apporte donc une réponse, en permettant à Airbus d’optimiser l’usage de la donnée et d’accélérer le passage du prototype virtuel au produit final. Cette démarche cadre aussi avec la volonté européenne d’indépendance technologique et d’excellence industrielle.
En s’appuyant sur les jumeaux virtuels, il est possible de tester divers scénarios de conception pour réduire le poids de l’avion, optimiser l’aérodynamisme ou encore étudier l’intégration de moteurs plus respectueux de l’environnement. L’objectif : diminuer la consommation en carburant et avancer sur la voie d’une aviation plus verte.
Les sept solutions clés proposées par Dassault Systèmes
Pour donner plus de consistance à cet accord, Dassault Systèmes met à disposition d’Airbus sept « industry solution experiences », qui sont en fait des ensembles de fonctionnalités spécialisés :
- Program Excellence : Permettre de gérer plus efficacement le pilotage des projets et les arbitrages tout au long du cycle de vie.
- Winning Concept : Concevoir rapidement des concepts d’avions et d’hélicoptères innovants, tout en intégrant la réalité du marché.
- Co-Design to Target : Synchroniser les équipes de conception autour d’objectifs précis de coûts, de délais et de performances.
- Cleared to Operate : Garantir la conformité réglementaire et la traçabilité, en particulier sur les aspects liés à la sécurité des vols et aux normes militaires.
- Ready for Rate : Gérer la montée en cadence de la production et anticiper les goulets d’étranglement.
- Build to Operate : Optimiser la fabrication, l’assemblage et l’intégration dans les usines, qu’il s’agisse d’avions civils ou de machines destinées à la défense.
- Keep Them Operating : Faciliter le suivi en service, la maintenance et la logistique, afin de prolonger la durée de vie et la fiabilité des appareils.
En rassemblant toutes ces briques fonctionnelles sur une unique plateforme, Dassault Systèmes entend proposer une expérience unifiée, où chaque département d’Airbus peut trouver et exploiter l’information dont il a besoin.
L’histoire de Dassault Systèmes : un éditeur au cœur de la transformation numérique
Créée en 1981, Dassault Systèmes est historiquement la branche logicielle du Groupe Dassault, qui avait alors besoin de solutions de conception assistée par ordinateur pour l’aviation. Rapidement, l’entreprise a pris son autonomie et s’est imposée comme l’un des poids lourds du secteur de la CAO/PLM (Product Lifecycle Management) dans le monde. Aujourd’hui, elle est cotée sur Euronext Paris sous le code FR0014003TT8 (DSY.PA) et emploie plus de vingt mille collaborateurs à l’international.
Sa philosophie consiste à créer des « mondes virtuels » afin de tester, innover et améliorer toutes sortes d’objets et de services. Cette mission, qualifiée par ses dirigeants d’« accélérateur de progrès humain », se reflète dans les solutions logicielles qu’elle propose : de la gestion des processus industriels à l’accompagnement des chercheurs en médecine, en passant par les projets urbains ou encore l’ingénierie mécanique.
Dans le monde aérospatial, Dassault Systèmes est à l’origine de technologies de conception qui ont déjà fait leurs preuves pour les avions militaires et civils. Son produit phare, CATIA, est utilisé depuis des décennies par les ingénieurs pour modéliser des pièces complexes. Aujourd’hui, la plateforme 3DEXPERIENCE s’appuie sur cette expertise historique pour proposer une suite logicielle complète, adaptée aux exigences modernes de connectivité et de collaboration en temps réel.
Bernard Charlès, actuellement Président du Conseil d’administration de Dassault Systèmes, est l’artisan de la mutation de l’entreprise vers la 3DEXPERIENCE. Sous sa direction, Dassault Systèmes a développé une approche globale, intégrant la gestion du cycle de vie produit, la simulation et l’innovation collaborative.
Airbus, champion européen face aux enjeux du XXIe siècle
Airbus, dont le siège principal se situe à Toulouse, est devenu un acteur incontournable de l’aéronautique mondiale. Avec sa gamme d’avions commerciaux (de l’A220 à l’A350, en passant par l’emblématique A320), le groupe s’est forgé une réputation de leader technologique. Il est aussi présent sur le segment militaire, notamment avec l’A400M, et assure le développement d’hélicoptères civils et de défense via Airbus Helicopters.
Les enjeux auxquels Airbus fait face sont multiples : maintenir son avance en matière de technologies d’allègement et d’avions connectés, tout en réduisant drastiquement les émissions de CO₂. Sur le plan militaire, la montée en puissance de drones et d’aéronefs furtifs appelle un renforcement de la recherche et développement, dans un contexte géopolitique instable. Le groupe doit donc trouver l’équilibre entre compétitivité, innovation et responsabilité environnementale.
Pour atteindre ces objectifs, la transformation numérique constitue un véritable levier de performance. En unifiant les efforts d’ingénierie, de production et de service client, le partenariat avec Dassault Systèmes s’inscrit dans la logique d’une entreprise qui cherche à être à la pointe du numérique. C’est, pour Airbus, la garantie de disposer des meilleurs outils afin de préparer les avions de demain.
Perspective industrielle : vers un nouvel âge de la conception
La collaboration Dassault Systèmes–Airbus cristallise plusieurs tendances fortes dans l’industrie. D’abord, la simulation prend une place de plus en plus prépondérante. Les outils d’intelligence artificielle intégrés à la 3DEXPERIENCE permettent de traiter d’immenses volumes de données et de prédire, avec un degré de confiance élevé, l’impact d’une modification de design ou l’effet d’un nouveau matériau.
Ensuite, la multiplication des prototypes virtuels réduit considérablement le recours à des maquettes physiques, coûteuses et souvent longues à fabriquer. Cette agilité accrue accélère non seulement les cycles d’innovation mais ouvre également la possibilité de concevoir plusieurs concepts en parallèle, en testant des configurations radicalement différentes.
Enfin, la gestion du cycle de vie se prolonge bien au-delà de la mise en service. Les données recueillies durant les vols, les entretiens et les retours de la clientèle sont réintégrées dans le jumeau virtuel, permettant un suivi continu de la fiabilité et de la performance des appareils. Cette approche de « conception en boucle fermée » (closed-loop engineering) crée un cercle vertueux d’amélioration continue.
Bon à savoir : la science des matériaux
Dans l’aéronautique, le recours à des composites et alliages spéciaux est décisif pour réduire la masse des appareils et améliorer leur résistance. Les simulations numériques peuvent désormais prédire la durabilité d’un matériau avant même qu’il ne sorte d’une chaîne de production.
Les retombées pour les fournisseurs et l’écosystème élargi
Au-delà d’Airbus, c’est toute la filière aéronautique qui pourrait bénéficier de ce changement d’échelle. Les principaux sous-traitants, qu’il s’agisse de fabricants de pièces mécaniques, de systèmes électroniques ou d’intégrateurs, sont encouragés à adopter les outils de la plateforme 3DEXPERIENCE. Cette standardisation numérique pourrait générer d’importants gains de productivité et faciliter les échanges de données entre les différents acteurs du secteur.
De plus, les exigences en matière de traçabilité poussent chaque fournisseur à documenter méticuleusement les composants livrés, leurs caractéristiques et leur cycle de vie. Les solutions numériques de Dassault Systèmes permettent de centraliser ces informations, contribuant ainsi à simplifier les processus de certification, notamment dans un secteur aussi réglementé que l’aéronautique. À terme, cette transparence accrue pourrait se traduire par une réduction des coûts et une meilleure réactivité face aux aléas de la production.
Enfin, le partenariat stratégique ouvre la voie à des collaborations renforcées dans d’autres projets européens, tels que le Future Combat Air System (FCAS), un programme de défense qui mobilise plusieurs pays et industriels. Il est probable que l’expérience acquise avec l’implémentation de la 3DEXPERIENCE dans les programmes Airbus puisse être étendue à d’autres coopérations.
Un regard sur l’avenir de l’aviation et les innovations de rupture
La modernisation des outils numériques intervient au moment où l’aviation cherche à se réinventer. Les technologies émergentes, telles que la propulsion à hydrogène, les batteries électriques ou encore la motorisation hybride, sont à l’étude pour réduire l’empreinte carbone des avions. Le recours à des jumeaux virtuels accélère grandement la recherche, en permettant de simuler toutes sortes de scénarios, depuis la combustion de carburants alternatifs jusqu’à l’agencement intérieur des cabines pour optimiser l’espace.
Airbus a déjà annoncé son ambition de lancer, d’ici une quinzaine d’années, un avion à zéro émission. Même si les détails exacts de cette initiative ne sont pas entièrement dévoilés, on sait que l’entreprise teste plusieurs configurations d’ailes et de moteurs destinées à embarquer des technologies non conventionnelles. On peut donc s’attendre à ce que la plateforme 3DEXPERIENCE joue un rôle déterminant dans la poursuite de ces recherches.
Parallèlement, l’usage de l’intelligence artificielle et des technologies de simulation avancées transforme également la manière dont les aéronefs sont pilotés et entretenus. Les capteurs répartis dans les appareils peuvent envoyer des données en temps réel, assurant une maintenance prédictive plus fine, réduisant les temps d’immobilisation et améliorant la sécurité des vols.
Coopération accrue : une dynamique durable ?
L’extension du partenariat entre Dassault Systèmes et Airbus ne se limite pas à un simple échange de licences logicielles. Les deux entreprises affirment vouloir construire un modèle de collaboration sur le long terme, où l’évolution des besoins d’Airbus influencera la roadmap de Dassault Systèmes, tandis que les innovations technologiques de Dassault Systèmes offriront à Airbus des capacités inédites.
Cette boucle de co-innovation est au cœur de la réussite de ce type de partenariat. Pour Dassault Systèmes, l’apport d’Airbus (et plus largement du secteur aérospatial) est une source inépuisable d’idées et de problématiques concrètes à résoudre. La plateforme 3DEXPERIENCE doit ainsi continuellement s’adapter pour suivre l’évolution rapide des exigences réglementaires, environnementales et techniques.
Au-delà de l’aviation, il est intéressant de noter que Dassault Systèmes collabore également avec d’autres industries (automobile, médecine, construction navale…). Les avancées issues du domaine aéronautique pourraient donc bénéficier à l’ensemble de l’écosystème industriel. On parle souvent d’effet de pollinisation croisée, où les progrès réalisés dans un secteur diffusent vers un autre.
Chiffres clés à garder en tête
Airbus : plus de 130 000 employés dans le monde, des centaines de clients compagnies aériennes et une présence industrielle sur plusieurs continents.
Dassault Systèmes : près de 40 ans d’expérience, plus de 370 000 clients répartis dans 140 pays, et de solides partenariats dans la recherche scientifique.
20 000 utilisateurs visés pour ce nouveau déploiement 3DEXPERIENCE chez Airbus.
Le potentiel de l’IA générative dans la conception aéronautique
L’un des volets clés évoqués dans l’accord concerne l’intégration de l’intelligence artificielle générative. Sur la plateforme 3DEXPERIENCE, cette technologie pourrait permettre de générer automatiquement des designs d’ailes ou de fuselages optimisés en fonction de critères prédéfinis, comme la résistance, le poids ou l’aérodynamisme. L’ingénieur n’a alors plus qu’à sélectionner la configuration la plus prometteuse, réduisant considérablement le temps passé à itérer manuellement sur différents concepts.
Ce procédé, encore émergent, ouvre des perspectives intéressantes pour concevoir des appareils plus légers et plus économes en carburant. Il pourrait également contribuer à renforcer la sécurité, en identifiant des configurations structurelles mieux adaptées à des contraintes extrêmes (turbulences, conditions météorologiques sévères, etc.). Cette utilisation créative de la donnée se rapproche de plus en plus des méthodologies de type « big data » adoptées dans d’autres industries de pointe.
De plus, l’IA générative va au-delà de la seule conception : elle peut soutenir la planification de la production ou la simulation des scénarios d’approvisionnement. Par exemple, en cas de pénurie d’un matériau donné, elle pourrait proposer des alternatives équivalentes ou signaler des fabricants susceptibles de fournir un substitut. Ainsi, la chaîne logistique gagne en résilience.
Un virage numérique qui pourrait inspirer d’autres secteurs
Alors que la transition numérique devient un enjeu incontournable pour toutes les industries, l’exemple Airbus-Dassault Systèmes illustre parfaitement la nécessité de repenser les modes de conception et de production. Avec la 3DEXPERIENCE, on assiste à l’émergence de plateformes holistiques, capables de centraliser, analyser et mettre à disposition un nombre colossal de données.
Au-delà de l’aéronautique, ce modèle pourrait être adopté par l’énergie, l’automobile ou encore la construction. Dans chacun de ces domaines, la modélisation et la simulation virtuelles permettent d’économiser des ressources, de réduire les délais et de limiter les risques liés aux essais physiques. L’interopérabilité des solutions logicielles reste néanmoins un défi crucial pour éviter que les industries ne se retrouvent enfermées dans des écosystèmes trop fermés.
En France, le soutien des pouvoirs publics à la Recherche & Développement et l’intérêt pour l’industrie du futur encouragent des initiatives similaires, où le numérique est vu comme un levier de renaissance industrielle. Les synergies entre grands groupes, PME innovantes et centres de recherche pourraient se multiplier, dopant l’attractivité du pays dans les domaines de l’innovation et de la haute technologie.
Un nouveau défi : intégrer la maintenance prédictive dans chaque étape
L’une des particularités de l’accord signé le 24 avril 2025 est de souligner l’importance du service après-vente et de la maintenance. En effet, le cycle de vie d’un avion s’étend sur plusieurs décennies, et son entretien représente une part majeure du budget d’une compagnie aérienne ou d’un opérateur militaire. La digitalisation de ces aspects, via la plateforme 3DEXPERIENCE, va donc bien au-delà de la conception initiale.
En récoltant et en analysant en continu les données de vol, il devient plus facile de repérer les signaux faibles d’une panne à venir. Une pièce présentant un taux anormal de vibrations pourra ainsi être remplacée de manière préventive, réduisant les temps d’immobilisation. Pour Airbus, cette approche permet de proposer à ses clients un service plus réactif, tout en améliorant la réputation de fiabilité de ses appareils.
Dassault Systèmes, de son côté, y voit l’opportunité de renforcer son offre « Keep Them Operating ». Cette solution, incluse dans les sept « industry solution experiences », a vocation à accompagner l’ensemble du cycle de vie opérationnel. Elle repose notamment sur des algorithmes d’intelligence artificielle capables de croiser les données de conception, d’assemblage et de performance en vol, afin d’améliorer en continu la définition du produit initial.
Un levier d’efficacité et de réduction des coûts
L’amélioration de l’efficacité et la maîtrise des coûts figurent au cœur de la stratégie d’Airbus. Dans un marché aéronautique où les compagnies cherchent à limiter leurs dépenses et où la concurrence est rude, le gain de quelques pourcents d’efficacité peut se traduire par des économies de millions d’euros. Cela vaut aussi pour la production d’hélicoptères et d’avions militaires, domaines où la rigueur budgétaire peut être tout aussi critique.
Grâce à la 3DEXPERIENCE, il devient plus aisé d’identifier les redondances dans les processus, de mieux calibrer les stocks de pièces détachées ou encore de rapprocher la conception et la production pour éviter de coûteux ajustements de dernière minute. Sur le plan organisationnel, la plateforme favorise une circulation des informations en temps réel, offrant à chaque ingénieur ou opérateur la possibilité de prendre rapidement des décisions éclairées.
Ces avancées technologiques s’accompagnent toutefois d’un défi humain : celui de la formation continue. Les métiers de l’aéronautique évoluent vers une utilisation plus poussée du numérique, ce qui implique d’investir dans l’acquisition de compétences. Cet enjeu peut être vu comme un coût supplémentaire, mais il représente aussi une opportunité de renforcer l’attractivité du secteur pour les talents.
Des retombées potentielles pour l’économie française
La participation de fournisseurs et partenaires basés en France et en Europe, intégrés à la plateforme 3DEXPERIENCE, pourrait avoir un effet d’entraînement sur l’ensemble de la filière. En démocratisant l’accès à des outils numériques de pointe, on améliore la compétitivité des entreprises de taille intermédiaire (ETI) et même de certaines PME. À terme, cela se traduit par un renforcement du maillage industriel français, un argument souvent avancé pour justifier le soutien aux grands programmes aéronautiques.
De plus, la création et l’entretien des jumeaux virtuels peuvent générer de nouvelles opportunités d’emplois spécialisés, aussi bien pour des ingénieurs que pour des développeurs de solutions logicielles. L’effet domino sur la formation initiale et continue en ingénierie, programmation et analyse de données ne doit donc pas être négligé. On peut s’attendre à voir émerger des cursus académiques ou professionnels davantage orientés sur la simulation et la modélisation 3D.
Enfin, l’image de la France en tant que pôle d’excellence dans les technologies industrielles se trouve renforcée. Les visiteurs étrangers, qu’il s’agisse de délégations gouvernementales ou d’investisseurs, pourraient être séduits par l’écosystème innovant autour de l’aéronautique et de la transformation numérique.
Perspectives pour la prochaine génération d’aéronefs
Le partenariat prolongé entre Dassault Systèmes et Airbus, scellé le 24 avril 2025, trace les grandes lignes de ce que pourrait être la prochaine génération d’avions civils et militaires. En offrant une plateforme digitale plus complète et plus intégrée, il ne s’agit plus seulement de gagner en productivité, mais aussi d’explorer des voies de rupture technologique. Les équipes d’ingénierie pourront imaginer des concepts d’aéronefs plus audacieux, incorporant l’intelligence artificielle, de nouveaux matériaux ou des systèmes de propulsion inédits.
Cette ambition s’inscrit dans un paysage aéronautique en pleine mutation, avec la pression pour réduire l’impact environnemental et le besoin croissant d’assurer la défense européenne face à des menaces de plus en plus sophistiquées. Les jumeaux virtuels deviendront alors le socle indispensable pour tester toutes les hypothèses et affiner les solutions, sans recourir systématiquement à des essais physiques onéreux et longs.
Si ce modèle fait ses preuves, on peut raisonnablement anticiper que d’autres consortiums industriels emboîteront le pas, non seulement dans l’aéronautique mais aussi dans d’autres secteurs où la virtualisation et la collaboration à grande échelle sont des facteurs clés de réussite.
Au-delà de la modernisation des processus, cette alliance symbolise une nouvelle ère dans laquelle le numérique et l’intelligence artificielle façonnent la conception, la fabrication et la maintenance de systèmes aéronautiques, ouvrant la voie à des progrès majeurs pour l’ensemble de l’industrie.